Product Catalogue
Air Compressors
40 products
Showing 1 - 24 of 40 products
Designed to provide compressed air to air tools, our range of air compressors include both electric compressors and petrol compressors (gas compressors). Produced with tank sizes ranging from as small as 3 litres, to as large as 270 litres, our compressors are manufactured by brands such as Ace & K, Bamax, MAX, Nardi and Senco. They are produced in a variety of different styles and sizes, covering you whether you require a smaller portable model, when working on a construction site for example, or a heavy duty stationary model, when working in a workshop for example. Regardless of whether you are using a lighter tool or a heavy duty tool, we have a compressor for you.












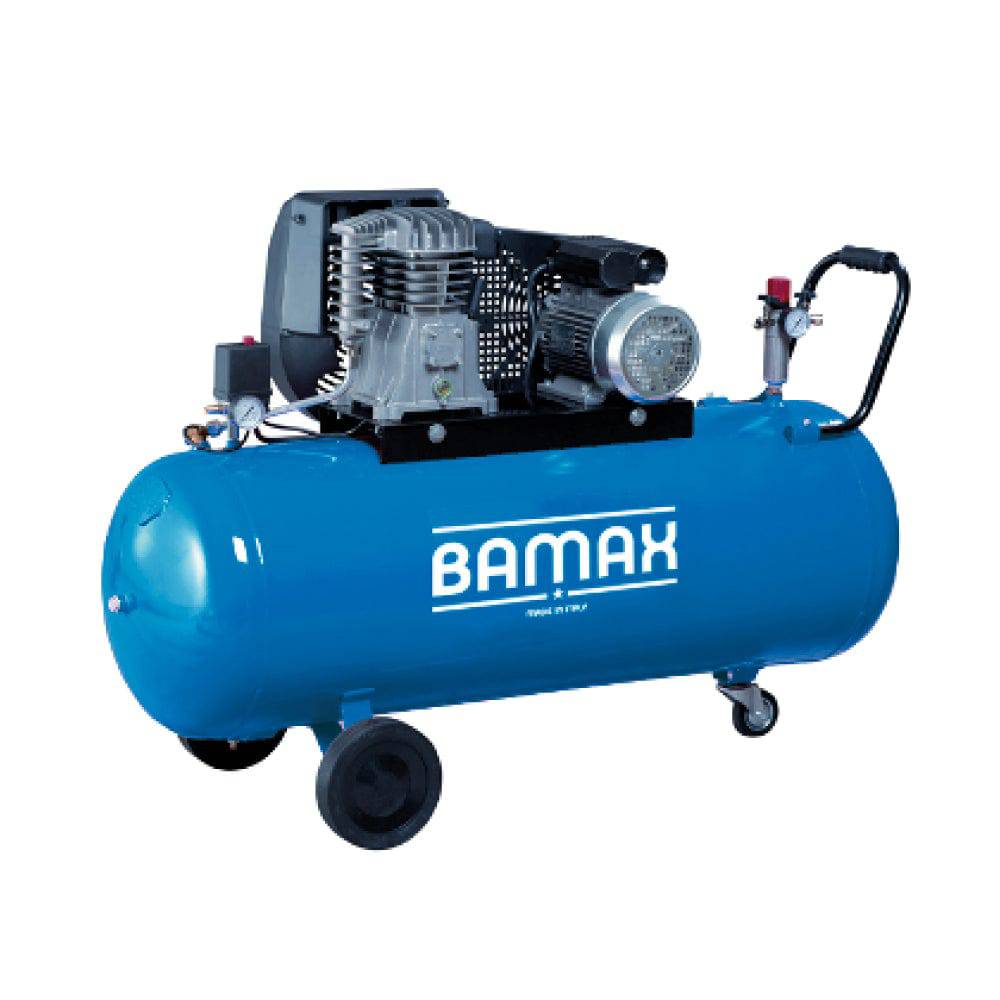



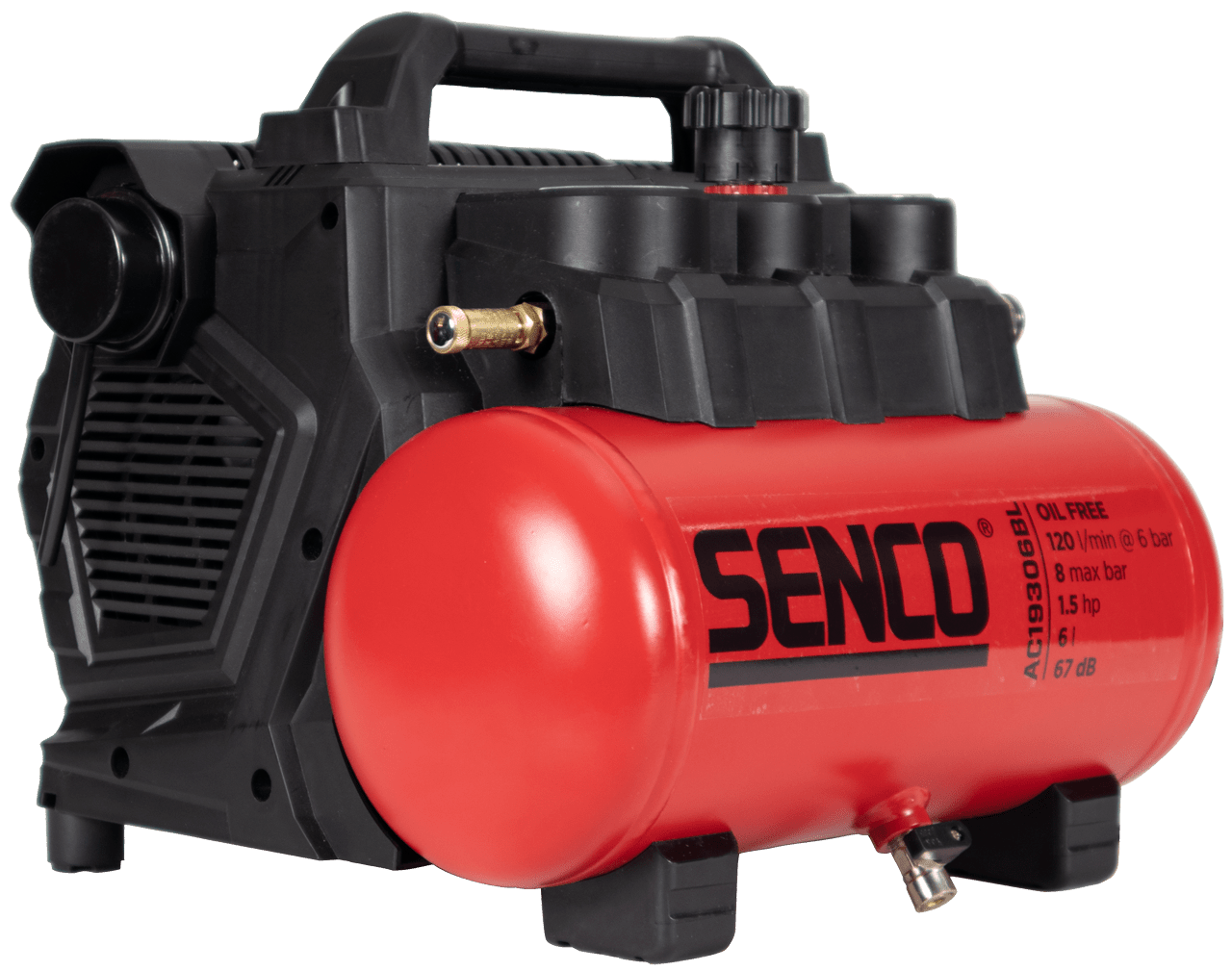





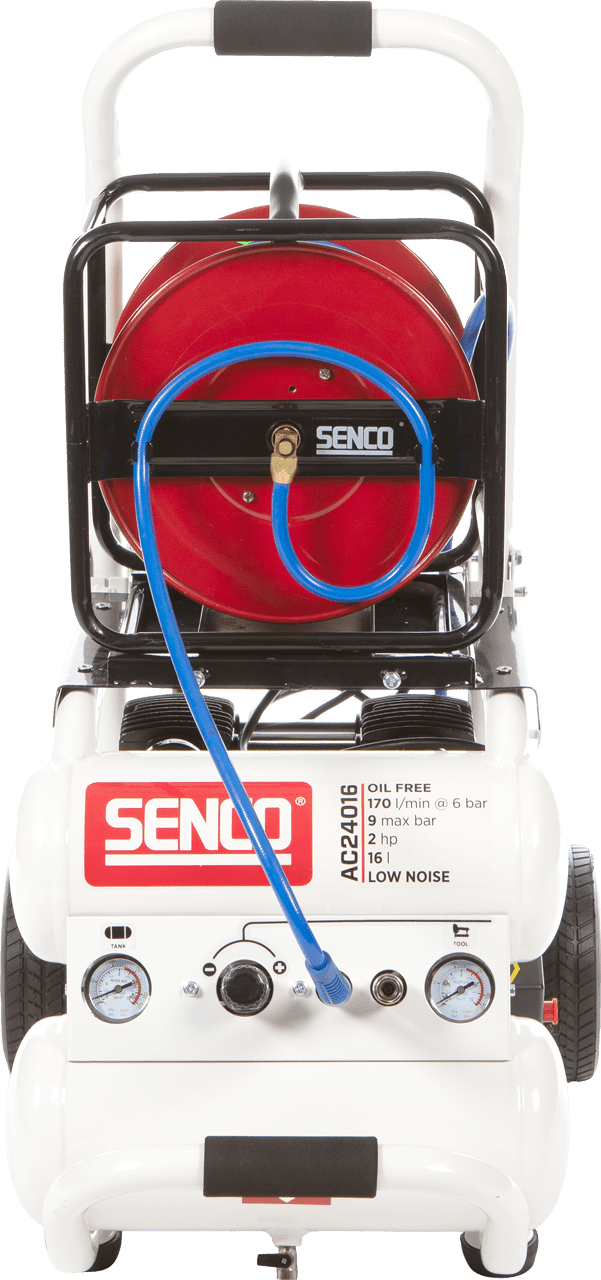
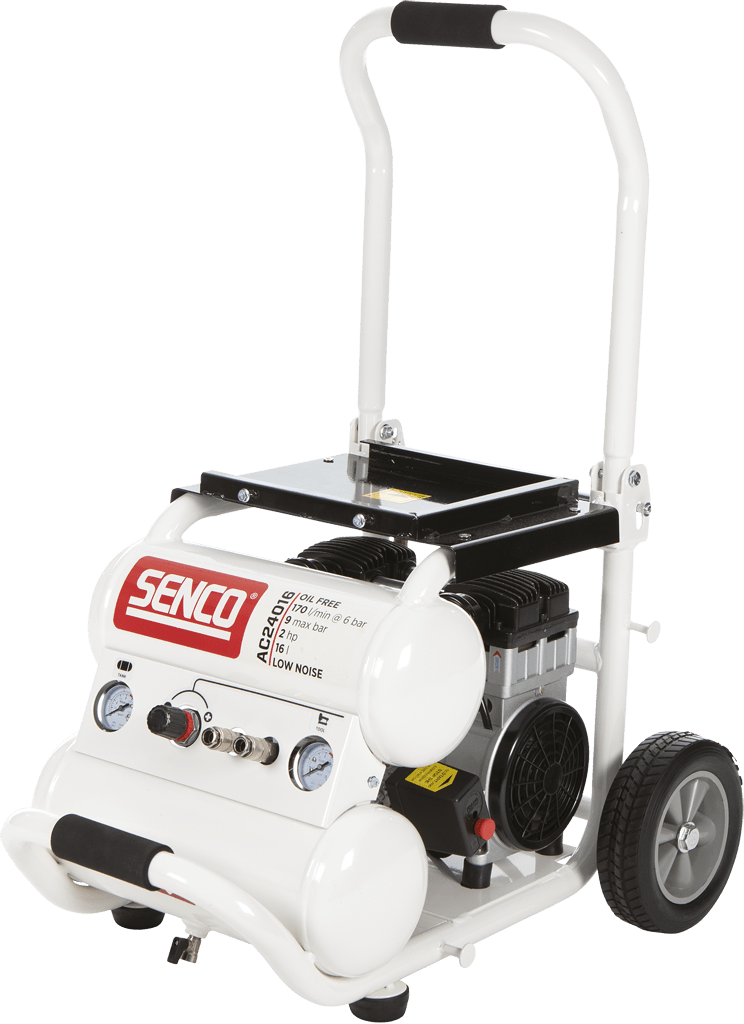

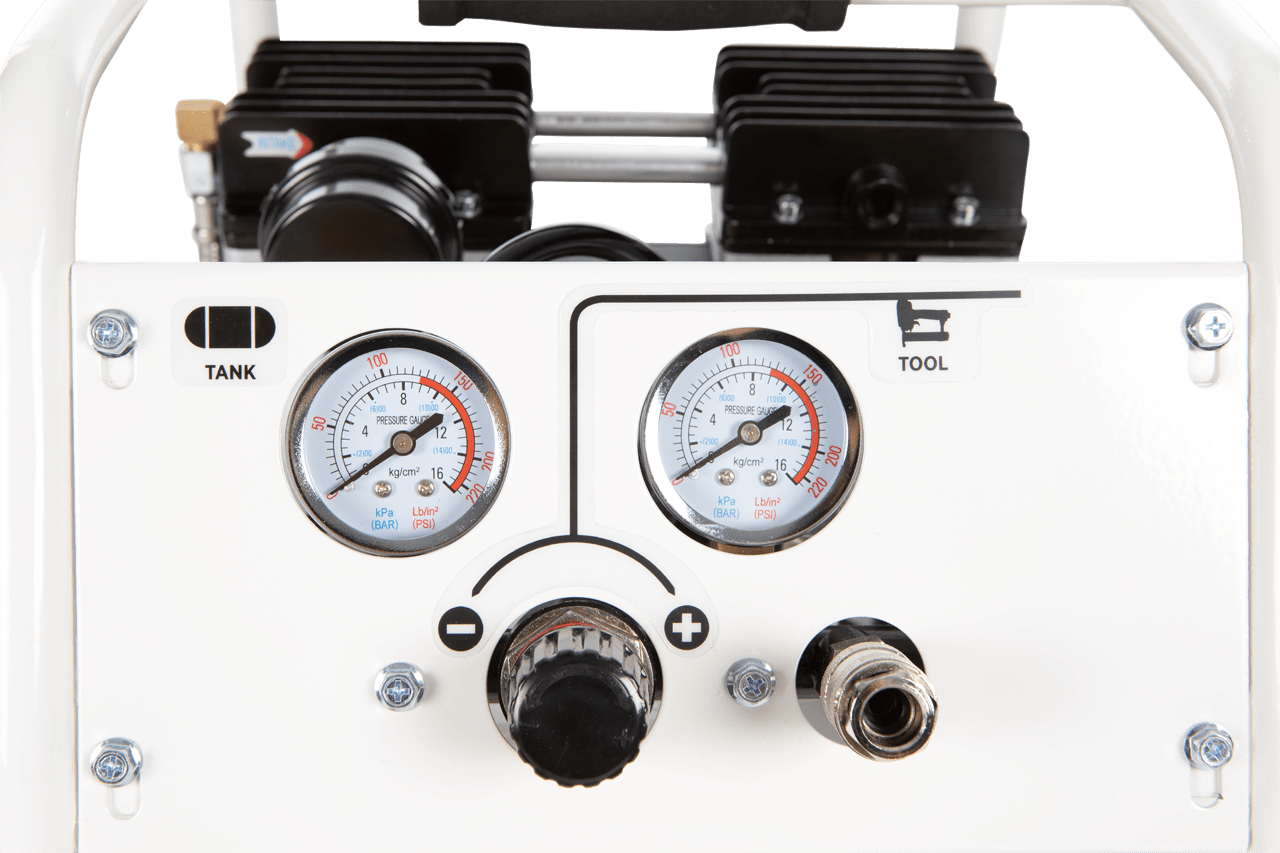










Types Of Air Compressors
Designed to provide compressed air to pneumatic tools, air compressors use a motor to suck surrounding air into their storage tanks, this continues until the storage tank reaches its upper limit, at which point the motor shuts down. When the trigger on a connected tool is pulled, compressed air is driven from the storage tank to the tool, via an air hose, which causes the tool to fire its fastenings. When the air pressure levels within the storage tank reach its lower limit, the motor restarts and refills the tank. The two most common types of motors used within air compressors are electric motors and petrol motors (gas motors).- Electric Air Compressor – Powered by an electric motor, electric air compressors are significantly quieter than petrol / gas compressors. They do however require a mains power outlet and therefore are less portable than petrol compressors. As a result, they are commonly used in areas where an electricity source is easily found, such as workshops, homes and buildings.
- Petrol Air Compressor – Powered by a petrol motor, petrol air compressors do not require an electricity source, meaning they are commonly used in remote areas where an electric air compressor may be unusable. They are however heavier and more cumbersome than their electric counterparts and also create more noise, although they do tend to provide more power, making them especially useful for heavier duty pneumatic tools where more power is required.
Portability:
When comparing portability between the two compressor types, it is first fair to say they both present elements of a portable air compressor. However, while an electric compressor is lighter, a portable petrol air compressor is more convenient, despite its size, as it does not require a potentially limiting mains electricity supply.
Air Compressor Features:
Other factors that influence the type of application an air compressor can be used for include the following:
- Storage Tank Size – The amount of air a compressor’s tank can hold at any one time. The larger a tank, the more tools a compressor can run at any one time and the heavier duty tools they can supply air to.
- CFM (Cubic Feet Per Minute) – The amount of air flow an air compressor can supply to an air tool. The CFM of a compressor should be higher than the tool being used requires, otherwise the user will have to take a break in between firing the tool to allow the compressor to resupply its air.
- PSI (Pounds per Square Inch) – The amount of air pressure that is being delivered to a tool. The PSI of a compressor should be sufficient to allow a tool to comfortably fire and penetrate the intended target, without any issues.